Third in an occasional series on ferrous mining in Minnesota.
United States Steel Corp. didn't think it was worth a public announcement, the news this month that at least one out of every four of its salaried employees would lose their job.
Among the roughly 750 employees now regarded as expendable were the general manager of its massive Gary Works steel mill complex in northwestern Indiana and its two top safety managers. Additional layoffs would be taking place at the company's operations in Europe.
These job losses are just another chapter in a corporate renewal program that U.S. Steel calls the Carnegie Way, named for the 19th century industrialist Andrew Carnegie. More than a clever brand for simply firing people, the Carnegie Way has meant pulling a lot management levers to get the company back to being an "iconic" American corporation and meet its goal of making an "economic profit" throughout the ups and downs of a business cycle.
It's been a painful process for U.S. Steel, with the idling of plants including the Keetac taconite facility near Keewatin, layoffs and the permanent shutdown of a mill in Alabama. The treasury and accounting function was outsourced and even a new corporate headquarters in Pittsburgh was put on ice.
Unfortunately, something just like this might be the only sensible plan for the future of Minnesota's iron mining industry. It's in need of ways to operate at lower costs, use less capital and deliver more than a raw material for the traditional blast furnace customers.
The news out of U.S. Steel over the last couple of years shows what a challenge the entire industry has on its hands. U.S. Steel has had only one profitable year since 2009. While it managed to have positive cash flow last year, it still reported a net loss of more than $1.5 billion.
It's not a self-inflicted wound for U.S. Steel, either. The net loss reached nearly $8 billion last year for ArcelorMittal, the world's leading steelmaker and one with big operations in the United States.
This latest industry downturn, driven by overcapacity of lower-cost steel and iron ore from places like Brazil, Australia and China, has been a reminder of how much the traditional American steel industry has lost ground.
U.S. Steel did not provide an executive to discuss its thinking, so it's unclear how much of the $815 million of cost savings and improvements attributed to the Carnegie Way program in 2015 came from its Minnesota taconite operations, including the state's largest in Mountain Iron. No one needed to explain why the company had to try something different.
It's been a long time since U.S. Steel was iconic, sitting atop the world's steelmaker ranking. It's lately slid to 15th. One observer pointed out that one of the company's biggest challenges is that it is still making steel in big batches using a basic furnace design patented in 1858.
For decades American executives enjoyed such a dominant position that they didn't need to look over their shoulders at the new ideas of competitors. As recently as the 1970s, U.S. Steel alone produced more than all the mills in China.
Unfortunately, operations across the industry became so bloated that in 1979, a year of strong demand that's generally regarded as the high water mark of the taconite era, U.S. Steel still managed to lose money.
A steep economic recession a couple of years later made the day of reckoning for the industry even worse. By 1984, steel industry employment had been cut more than half in 10 years, down to just more than 200,000.
"That is the precedent for what we're going through now, that '82 through '84 period," said Peter Kakela, a Michigan State University professor who has written extensively on the iron mining industry. "There was the threat of Brazilian iron ore coming up the Mississippi River on barges. Their claim was they could deliver iron ore cheaper than people could even load it in Minnesota."
The industry responded by cutting costs sharply. The big difference-maker turned out to be labor productivity, as what workers produced in an hour of work surged. That big turnaround was the subject of a well-known Federal Reserve Bank of Minneapolis study, with the author still marveling years later that the work rules in taconite production once kept operators from lifting a finger to set up, maintain or fix a machine, even simple repairs.
With fewer workers doing more, employment declined from a peak of close to 15,000 on the Iron Range in the late 1970s all the way down to around 4,000 in 1987, even though production volumes had partly recovered from the depths of the early 1980s recession. Kakela described the job losses as so painful that in 30 years the wounds in Minnesota haven't fully healed.
"Then they were running for a long time, like maybe 20 years, with almost no cost of production increase at all," he said. "Once worldwide demand increased and ore prices started to increase, I would guess the costs nearly doubled."
Efforts to now reduce costs in northeastern Minnesota have included negotiating lower royalty rates for mine production and idling higher cost operations. The industry sought, and was denied by the state's utility regulator, lower electricity rates that would have meant higher rates for residential customers.
The steel industry also, of course, has pushed for tariffs to slow down the flood of imported steel. In a complaint filed last summer over "unfairly traded" corrosion-resistant steel, American producers identified 48 different subsidy programs for producers in China, 88 in India, 12 in Italy, 43 in Korea and 22 in Taiwan.
But even easily justified protectionism isn't a good long-term solution for the American steel industry, according to the economist Toby Madden, a longtime Minneapolis Fed staffer now with consulting firm Power Parametrics.
Boosting prices for domestic steel helps out iron and steel firms but hurts the industries that consume steel, like American manufacturers. Consumers happen to be a far bigger part of the economy than producers, but his point is that our manufacturers could lose ground to their foreign-based competition if they have to pay higher prices for their steel. It might be enough to encourage them to try building their products abroad.
The only real path to a long-term recovery for American producers, including the raw material suppliers in northeastern Minnesota, is to come close to matching the efficiency of imports and beating them in other ways, such as superior customer service.
That's a tall order, as the Chinese steel producers in 2014 made about 10 times as much steel as the industry did here, supplied by cheap Australian ore. And much of China's new capacity came from mills built during the industrial boom of the 2000 to 2014 era.
"Now they're looking to cut production of steel," Madden said, of the Chinese. "When they cut it they are going to cut the least-efficient producers. And if they have been building all this new stuff in the 2000 and 2014 time period, these [remaining ] producers are probably not using 1800s technology."
lee.schafer@startribune.com • 612-673-4302
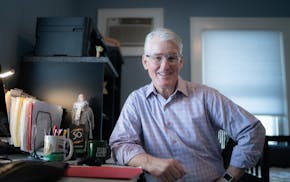
Schafer: What do you really need to retire?
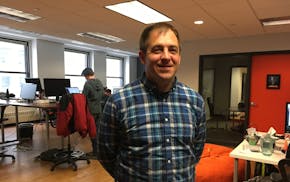
Schafer: How doing business can be a bit more like Christmas morning
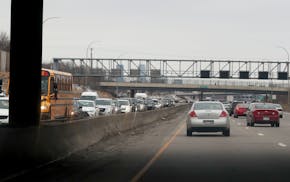
Schafer: There won't soon be another opportunity to rethink the I-94 corridor
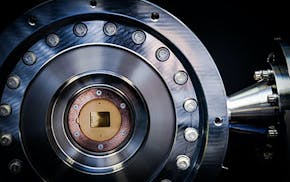
Schafer: The fruits of Honeywell's long-game dedication to quantum computer now being seen
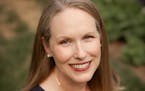