Despite national unemployment that tops 9 percent, American manufacturers insist they cannot fill 600,000 jobs because job applicants lack the high tech skills needed to run the country's factories.
That's the beef of 1,123 U.S. factory heads who were recently surveyed by The Manufacturing Institute and the accounting giant Deloitte LLP.
The manufacturing executives said that 5 percent of jobs inside their factories go unfilled because candidates are unqualified. They insist they need a highly skilled and flexible workforce in order to grow. Some admit they are stuck.
"The survey shows that 67 percent of manufacturers have a moderate to severe shortage of available qualified workers," said Deloitte Industrial Products Leader Craig Giffi. Sadly, some 56 percent of surveyed respondents anticipate that skill shortages will worsen in three to five years.
That's not good. After all, some 26 million Americans are currently unemployed or underemployed. People need jobs.
So what skills are lacking? "Skilled production workers " and "problem solvers" make up the broadest categories.
Actual job titles fall under names such as machinists, operators, craft workers, distributors and technicians, explained Manufacturing Institute President Emily DeRocco. "Unfortunately, these jobs require the most training and are traditionally among the hardest manufacturing jobs to find existing talent to fill," she said.
The trend accelerated in 2008 because many factories responded to the economic downturn by redesigning, automating and streamlining their production lines. So just as the industry changed, the skillset of workers needed to change as well, DeRocco said.
Minnesota manufacturers have long struggled with the problem. Some partner with community and technical schools to create training programs. Others snatch up retraining money from the state. And still others simply go without and won't invest in in-house training due to concerns about cost and an unforgiving economy.
Still, companies do nothing at their peril, insist experts.
"The results of this survey may appear dire," said Deloitte Consulting principal Tom Morrison. "Many manufacturers are using the same approaches to talent development as they were a decade ago. But new performance tools and formal processes like industry certifications should be playing a larger role in any talent management plan."
In heated western Minn. GOP congressional primary, outsiders challenging incumbent
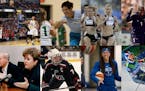
Minnesota Sports Hall of Fame: A class-by-class list of all members
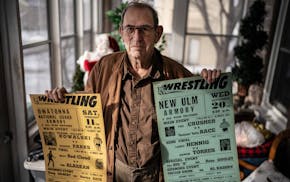
This retired journalist changed professional wrestling from Mankato
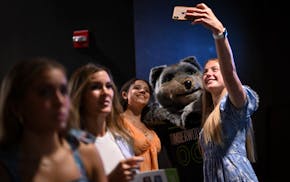