In the coronavirus pandemic's early days, engineers at the University of Maryland had been helping ActivArmor of Pueblo, Colo., develop custom 3-D-printed casts to help set broken bones.
Could the company pause and make custom masks, the engineers wondered?
It could — and they could be clear, reusable, form-fitting without any bruising and protective N95-grade.
"Everyone just wanted to do something to help," said William Bentley, of the university's engineering school. "We designed, built and tested masks, and ActivArmor made them."
The urgency to produce more masks has dropped as mandates eased around the country. But no one thinks omicron is the last dangerous coronavirus variant or the final pathogen to emerge.
The break from mask-wearing requirements offers researchers an opportunity to turn their attention to innovation, so that during the next coronavirus wave or a new pandemic, health care providers, first responders and the public have something better that what's available now.
There has been little change or innovation in masks for decades, though there are nascent efforts in the public and private sectors to develop a more perfect mask — one that is protective, comfortable, reusable and affordable.
Officials at ActivArmor and the University of Maryland institute think they are on to something.
"There is no reason to start from scratch," said Diana Hall, president and CEO of ActivArmor, which patented the design and sold 10,000 masks in a year.
The company has since returned to its core business of custom-printed waterproof casts.
For its masks, engineers had people scan their faces with an iPhone app and made 3-D-printed molds in their lab in Maryland. Then, a kind of clear, flexible plastic was heated and formed on the molds to make the actual masks.
Other masks sold were made in six preselected sizes, a range that meant just about everyone found one that fit.
Hall wants to hand off the project to a large-scale manufacturer and distributor. She believes other firms could use the heat-forming technology, the kind used to mold Solo plastic cups, to make masks for a couple of dollars each.
The six sizes can still be ordered through a company called HMD Technology in Canada, but Hall said they are expensive at $65 and up.
Government and industry officials hope some new thinking could increase uptake and reduce costs for when masks are again recommended or required.
"In the future, we need more effective and well-fitting masks," Dr. Eric Toner, a senior scholar at Johns Hopkins Center for Health Security, said during a recent webinar hosted by the center and the Steering Committee on Pandemic Preparedness and Health Security.
Historic $7.8M jury award in death of Minnesotan struck by driver who was high from huffing aerosol
A wild orangutan used a medicinal plant to treat a wound, scientists say
Remote Lake Superior island wolf numbers are stable but moose population declining, researchers say
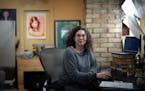