Not yet in her teens, Ellie Nadeau received upsetting news: the curve in her back was severe enough that she might need surgery.
The prospect of that potentially painful and lengthy ordeal brought Nadeau to a hospital examination room at Gillette Children's Specialty Healthcare, where a team of technicians had fashioned an alternative.
A binding brace, known as a TLSO for thoracolumbosacral orthosis, could halt the worsening of the S-curve in her back. But for up to 23 hours a day, for at least a year, she would be encased in plastic from her hips to her armpits. She would need to learn new ways to stand and sit.
And there would be regular clinic visits to tweak the brace to make sure it was applying the right pressure to help shape the growth of her spine. Getting the fit just right could be the key to a surgery-free future.
"Part of my job is to balance correction ... with comfort," Kristin Smith, a certified orthotist, explained as she inspected Nadeau's brace. "If she wears it and her arm pit is super-red, and she says it is falling asleep, then we will tweak it ... But if we trim [under the arms] too low, then we are not even effectively controlling the curve. So that's the balancing act."
It's a balancing act that orthopedic experts at Gillette have been performing for more than a century. Founded by an orthopedic doctor as a state-funded hospital, Gillette Children's today runs a self-sustaining network of clinics anchored by a main hospital in downtown St. Paul, generating more than $200 million in revenue.
More than 9,000 patients, about a third of the hospital's total, are served by its assistive-technology department, or ATD, which specializes in custom orthopedic devices for the spine, legs and skull.
Well-designed braces can mold kids' bones while they are still growing. But influencing that growth requires devices to fit precisely and be worn often — two major challenges for growing kids who can be easily irritated.
Gillette's staff of 68 certified orthotists, prosthetists and device technicians create or customize the devices by hand, meeting the physical-design requirements of the prescribing physicians, while letting the young patients and families select custom exterior designs.
Nadeau's TLSO is blue and bears a spirit-lifting Spider-Man logo that she picked out. ATD manager Bradley "BJ" Fisher said a major goal of Gillette's elaborate customization system is to give young patients a sense of ownership of their devices to make them more interested in using them. "The brace that sits in a closet doesn't really work very well," he said.
A bustling lab
The sounds of grinders, hot-air blowers and filtration systems fill the device workshop down the hall from Fisher's office as a dozen staffers work amid benchtop vices, gray shop stools and workstations not unlike those in a high school shop class.
A large oven that looks like it could cook a pizza waits to soften sheets of plastic for molding over plaster casts into TLSOs like Nadeau's. A small 3-D printer sits on a workbench not far from a century-old industrial sewing machine used to stitch Velcro straps onto tough materials.
Work in the device lab can run at a hectic pace, owing to the nature of the patient population that comes here. Some patients are referred from a doctor visit that day, others come from inpatient surgery and still others need a device before they can be discharged from physical rehabilitation.
"Sixty percent of the patients we are going to see today, we don't know where they are coming from," Fisher said one recent morning. "So we are staffed accordingly to handle that kind of MASH unit" frenzy.
Janet Cortes, a certified orthotist who specializes in spinal braces at Gillette, said that though it can be tough to see young children dealing with serious medical problems, the kids themselves tend to be happy to see the clinicians and to pick the colors and designs for their braces.
"It makes you feel good about what you are doing," Cortes said. "It makes you feel grateful about your life."
Orthopedic pioneers
In 1897, Dr. Arthur Gillette was a specialist in the then-nascent field of orthopedics when the Minnesota Legislature granted him authority to provide care at the University of Minnesota for the state's disabled children. Over the years, the hospital moved locations and named itself after its founding doctor.
Today, Gillette leases a floor from Regions Hospital; it is not formally affiliated with the HealthPartners-owned adult medical center. Gillette also runs a network of 11 clinics in the Twin Cities and around the state.
Gillette competes with two other children's hospitals in the Twin Cities metro to fill its 60 beds. Overall it handles 2.9 percent of the pediatric business in the Twin Cities, according to a 2016 analysis by Standard & Poor's, but 96 percent of the market in rehabilitation — 50 percent in orthopedics and 25 percent in neurology.
A not-for-profit, Gillette reported earning a 4 percent margin on $243 million in revenue in 2016.
Like other medical device makers, Gillette doesn't talk publicly about its pricing or product volumes. But TLSOs, ankle-foot orthoses, custom mobile chairs and CranioCaps — Gillette's trademarked version of baby helmets — are some of the most common devices seen in the department.
Molding young heads
Tuesdays, in particular, tend to be busy days for CranioCap scans.
Sarah Rahn and Tyler Mixson came to Gillette on one recent Tuesday on a visit that included having their 7-month-old son Luke's head mapped. Luke sat on Tyler's lap and watched a video clip of Joan Osborne's hit song "One of Us" as laser light from a handheld scanner traced the outside of his head, gathering data points that appeared as a blob on a screen behind him.
With each pass of the scanner-laser, the blob on the computer screen started to look more like Luke's small head. The goal was to create a 3-D printed mold of Luke's head, which would then be used to fashion a custom CranioCap. Luke's doctor said his skull is flat by a few millimeters in back, and a device like this would allow the bone to grow into a more natural shape over time.
Insurance covers the devices about 90 percent of the time, but ultimately Rahn and Mixson said they opted not to get a CranioCap for Luke. Rahn said Luke's head didn't seem that bad to her, and she hadn't even noticed the flat spot until the pediatrician mentioned it to her.
"I really didn't want the helmet to get in the way when I snuggled him," she said later. "I like kissing the top of his head and feeling him lean his head against my shoulder."
Elsewhere on the hospital floor, Katie Jensen was nearing the end of her daughter's CranioCap journey.
Jensen's 7-month-old daughter, Evelyn Shenefield, had been wearing the device for nearly three months, returning to the clinic every two weeks to get it adjusted. Initially, she wasn't sure she wanted to get the CranioCap for Evelyn, but she went forward with it after getting a second opinion from another doctor.
Now that Evelyn's been wearing it, her doctor says the progress is continuing as expected with each checkup, and so on this Tuesday, the back of the CranioCap was expanded to make room for further growth.
Evelyn sat on Jensen's knee and watched passers-by in the hall as her white CranioCap gleamed under the hospital lighting. If all went well, she would be done with the cap in a few more weeks, emerging with a more normal-shaped head and no memory of the months she spent wearing a custom-made skull orthosis.
"They said it was a good time to get it, when she was 5 months, because your head is still growing," Jensen said. "It's just a part of life when they're wearing it."
Joe Carlson • 612-673-4779
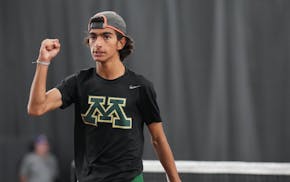
Fall or spring, it's Rochester Mayo's year in prep tennis
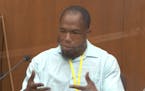
Minneapolis reaches $150k settlement with eyewitness of George Floyd's murder
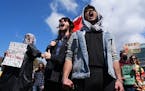
Israel-Hamas war creates 'really fraught times' at Minn. colleges
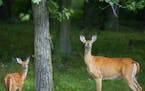
Rare and fatal brain disease in two deer hunters heightens concerns about CWD
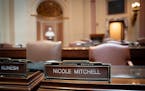